Fire Suppression for Agriculture Machinery
Agriculture can be a surprisingly delicate operation. Relying on many critical, expensive, and highly complex pieces of machinery that all need to work in harmony, a fire in any one of these machines can be catastrophic.
When working in confined areas – often packed with highly flammable materials like straw and grain (which produces combustible grain dust) – the smallest spark can rapidly spread out of control. This puts expensive business assets and human life in extreme danger, especially in storage buildings where egress can be complicated. When operating in fields, a fire can put an entire season’s crop at risk, which comes with obvious financial consequences.
There are many challenges when trying to protect against agricultural fires. However, there are also many steps that can be taken to overcome these challenges.
The Challenges
The environments that farming machines operate in are often full of highly combustible materials. Hay, grain dust, wood chippings, packing materials, biomass, and other materials can act as fuel for fires to spread quickly.
Without – and sometimes even despite – regular maintenance, these substances can build up around sensitive machine components. On a machine like a tractor, there is a high number of sensitive components, ranging from hydraulic fuel pumps, hoses, batteries, and electrical equipment situated alongside high heat sources like particulate filters and torque converters.
When the machine is running, the heat generated by these components can easily cause a fire to ignite even without an electrical failure. When adding those potential electrical failures into the conversation, the case for an automatic suppression system becomes clear.
As agricultural machinery can be large and loud, particularly in the case of specialist equipment like combine harvesters, an operator may not notice a fire has broken out until it has already spread out of control. An automatic system instantly works to suppress a fire at the point of ignition, but specifying the optimal solution for use on farmland machinery comes with its own challenges.
Specifying a Fire Suppression System
The machinery used in modern agriculture is simply too diverse for a one-size-fits-all fire suppression solution. Packing machines, conveyors, and other static machinery require a completely different protection system than tractors and bale wrappers. Likewise, modern battery-powered vehicles should make use of a different suppression agent than their traditional ICE equivalent.
For many static, indoor machines, a pneumatic fire detection solution will likely provide adequate protection. These systems use a pressurised tube routed around every potential fire hazard in a machine. Once a fire breaks out, the heat will rupture the tube, causing the suppression agent to be dispersed through that rupture. An elegantly simple solution, pneumatic systems are unpowered, meaning they will still deploy in the event of a power outage.
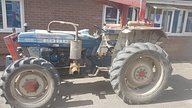
However, they are not a universal solution. Some farm machines, like tractors, have to contend with difficult conditions – which means their fire suppression systems do, too. Extreme weather, constant vibrations and impact shocks, and chunks of debris thrown up from the land are just a few potential issues that can cause damage to a pneumatic tube. If the tube is damaged to the point that it ruptures, it will discharge. In some cases, a false discharge can cause a comparable amount of damage and downtime to fire. As one of the key jobs of a fire suppression system is to protect against excessive asset damage, this can defeat the point of installing one in the first place.
A system that can differentiate between fire and other causes of damage is therefore the ideal solution. We recommend a linear heat detection (LHD) cable system for mobile plant, outdoor machinery, and agricultural vehicles. An electrical system, the LHD cable is made of copper wires coated with a heat-sensitive polymer. Once a flame ignites, it will melt the polymer and cause the wires to contact, sending a short-circuit to a control module to deploy the suppression agent.
Crucially, the LHD system only deploys in the event of a fire – it does not deploy if the cable is kinked, cut, or damaged by other means. If it does get damaged, it is relatively quick and easy to replace, minimising downtime. This makes it a more reliable solution for vehicles that have to cope with more testing conditions.
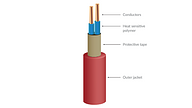
Which Suppression Agent Should Be Used
Again, the choice of suppression agent is highly dependent on application, and decisions should be made on a case-by-case basis. For example, any electrical cabinets or battery compartments should not be protected by a wet, water-based suppression agent.
Often, a dual agent solution is recommended, as there is no single perfect suppression agent. A dual agent system, as the name suggests, uses two different agents, with the strengths of one covering the weaknesses of another.
For example, in the event of a fire on board a tractor, we may recommend a combination of dry powder (ABC chemical) and wet agents. The powder discharges quickly and offers the fastest extinguishing time. However, tractor fires also have to contend with the risk of re-ignition, particularly if fossil fuels are present. The wet chemical offers limited extinguishing capabilities, but it is excellent at cooling down superheated components and preventing re-ignition.
Installing fire suppression systems on farm machinery
Every install is different, which is why we conduct a thorough five-step evaluation – including an on-site analysis – before each installation. Agricultural machinery is varied in design and application, and each one poses its own unique challenges. Does it work to process combustible material? Does it need to cope with extreme weather? Will it be left running without supervision for extended periods? The list of questions seems endless. The only way to comprehensively answer them is by utilising the services of a safety expert like Ardent, who will conduct a thorough hazard analysis on-site.
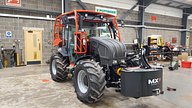