Mobile plant fire suppression systems
Making sure mobile plant fire suppression systems are installed to fit the application and operating conditions of equipment in an organisation is the first step in securing safe protection for lives and livelihoods.
We want to help businesses make this crucial decision by providing them with in-depth information about mobile plant fire suppression systems and how they work, so companies can be confident they made a safe and reliable choice.
From agriculture to construction, mobile plants working in harsh environments are often subject to significant shock and vibration as well as temperature swings. Therefore, it’s vital that mobile plant fire suppression systems can reliably maintain the protection and performance expected from them.
Why electronic mobile plant fire suppression systems?
1. Electronic fire suppression systems are proven to offer the best performance and higher level of reliability in mobile plant applications. Heavy shock and vibration (commonly seen in industrial environments where off-road vehicles operate) requires robust mobile plant fire suppression systems that can perform under these challenging conditions.
2. Electronic fire detection technology significantly reduces the likelihood of false discharges, which result from loss of pressure commonly seen in pneumatic fire suppression systems. Given that gas will always leak through a seal over time (made worse by temperature), there is a risk that the tube pressure will drop, leading to a false system discharge. Ancillaries such as pressure switches and manual actuators introduce additional connections, increasing potential leak points. This, compounded with a high-vibration environment subject to massive temperature swings, further decreases the reliability of pneumatic systems.
3. Electronic mobile plant fire suppression systems can differentiate a signal caused by damage to the detection cable from a fire signal, and the system will only activate in the latter scenario. In addition, electronic systems constantly monitor the state of the fire detection cable and alert the operator of any damage so it can be rapidly rectified.
At Ardent, we take care to ensure mobile plant fire suppression systems are the right choice for every application. This includes performing a thorough fire hazard identification on equipment before we design and specify a system based on a specific machine, its environment and working conditions, and individual business requirements.
How our electronic mobile plant fire suppression systems work
1. High temperatures are detected, fast
Ardent mobile plant fire suppression systems utilise electronic fire detection technology in the form of our Linear Heat Detection (LHD) cable. The LHD cable is routed around all identified fire hazards in the machine to detect a fire or elevated temperature condition within seconds, initiating the fire suppression system discharge.
This fire detection cable is designed to reduce false discharges to a minimum, while providing live monitoring capabilities.
- Increased reliability
The LHD cable significantly reduces potential false discharges commonly seen in pneumatic systems used in mobile plant. - Live status monitoring
The system communicates any detection cable damage and alerts the operator via the control module. - Detection isolation
The fire detection circuit can be isolated for machine maintenance, allowing the system to still be activated manually if needed.
How the LDH cable works
A heat sensitive polymer coats the conductors and melts when exposed to the heat generated by a fire or elevated temperature condition. The LHD cable is designed to initiate the system discharge at 180°C. Some systems are designed to detect and discharge at lower temperatures - however ambient temperatures in mobile plant may reach or exceed the lower temperatures required for system activation, resulting in higher instances of false discharges.
When the heat sensitive polymer melts, the conductors are exposed. These initiate contact with one another, resulting in a short-circuit signal being sent to the Ardent VCM control module and initiating the system activation.
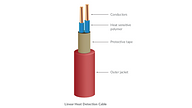
2. The system is activated
The Ardent VCM control module acts as the brain of mobile plant fire suppression systems, handling fire detection, system discharge, system monitoring and alerts, and other functionalities.
The control module constantly monitors mobile plant fire suppression systems for fire signals, damage, and faults, providing visual and audible alerts to machine operators. Through this control module, operators can manually activate the fire suppression system or delay the automatic system activation. It also allows the system to be put in isolation mode for machine maintenance.
In addition to the VCM control module, manual activation point(s) provide the operator or other personnel with the ability to activate mobile plant fire suppression systems from outside the machine.
Optional time delay
The Ardent VCM control module can be configured to discharge the system following a predetermined time delay. This allows the operator to stop the machine safely, before the system discharges. The delay period can be configured according to individual needs and preferences.
Engine shutdown
Our mobile plant fire suppression system’s engine shutdown interface significantly reduces the chance of fire re-ignition after system discharge.
Fuel or hydraulic fluid leaks are a common cause of fire among mobile plant. When a fuel or hydraulic line (or connection) fails, it can spray fluid onto a superheated component such as a turbocharger or exhaust manifold, starting a fire. If the engine continues to operate, this fluid will continue to fuel the fire. The engine shutdown stops the intake of more fuel by the engine, stopping the ignition of fuel or other flammable fluids coming into contact with superheated components.
Battery isolation
Electrical faults are a main cause of vehicle fires. This is why we recommend installing an automatic battery isolator, which reduces the chances of an electrical fire re-igniting. Battery isolation units automatically switch off the battery when mobile plant fire suppression systems are activated, reducing the risk of damaged wiring re-starting the fire.
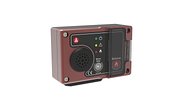
Ardent VCM Mk 2 Control Module
3. Suppression agents are dispersed
The most common suppression agents used in mobile plant fire suppression systems are dry chemical, also known as ABC powder, and wet chemical - either AFFF (Aqueous Film Forming Foam) or other liquid-based agents.
- Dry chemical suppression agents offer reliable fire knock-down and excellent coverage of the protected areas. Thanks to its powder form, this agent hits the fire with high intensity and disperses easily, aiding coverage of the hazard areas. Dry chemical is proven to be three times more effective than wet chemical at extinguishing fires on a weight-for-weight basis.
- Wet chemical suppression agents have limited fire suppression capabilities, but do excel at cooling. Wet chemical agents provide effective cooling of superheated components, such as turbochargers and exhaust manifolds. This reduces temperatures below the autoignition temperature of diesel and other flammable fluids, significantly reducing the risk of fire reignition.
For large mobile plant, we always recommend an Ardent Dual Agent Fire Suppression System. These systems combine dry and wet chemical suppression agents to provide rapid and reliable fire suppression, as well as cooling to further protect against fire reignition.
-
Increased reliability
The LHD cable significantly reduces potential false discharges commonly seen in pneumatic systems used in mobile plant.
-
Live status monitoring
The system communicates any detection cable damage and alerts the operator via the control module.
-
Detection isolation
The fire detection circuit can be isolated for machine maintenance, allowing the system to still be activated manually if needed.
Agent storage tanks
Every machine is different and finding the right location for agent tanks can sometimes require creative solutions. At Ardent, our wide range of agent tank sizes allows us to provide a flexible system specification. This way, we can find a solution to protect all plant, great and small.
Our dry chemical suppression agent tanks range from 6kg to 24kg and include a range of lay-flat tanks that can be installed horizontally. Lay-flat tanks offer the flexibility required for installation on smaller pieces of plant such as forklifts, where install space is limited and vertical tanks can impact an operator's visibility. Our wet chemical tanks also come in a range of sizes, starting at 7.3 litres and ranging up to 39.7 litres.
Agent Distribution Network
A mobile plant fire suppression system’s distribution network strongly influences the efficiency and speed of fire suppression. First, our system design determines the fire hazard areas to be covered by the discharge nozzles, carefully considering obstructions and the distance from the hazard. Then, a network of hoses and pipework carries the suppression agents from the agent tanks to the discharge nozzles.
For reliable fire protection, the nozzle’s pattern and maximum effective discharge range must be considered to ensure the discharge allows all fire hazards within the machine to be covered. Some areas may require multiple nozzles for sufficient coverage, while other hazards may be close enough that one nozzle is enough to cover them.
Mobile plant fire suppression systems tested to international standards
Ardent fire suppression systems for mobile plant applications are designed and engineered to withstand the most challenging conditions. This includes extensive internal and external testing, as well as obtaining accreditations and certifications to demonstrate our commitment.
Our mobile plant fire suppression systems achieved the A+ rating for the P-Mark SPCR 199:2021 certification - the highest rating for this testing. In addition to fulfilling the requirements of the standard, Ardent undertook tests at a higher severity than what is called to be awarded an A+ rating, showing our commitment to delivering market-leading system performance and reliability.
Ardent dual agent fire suppression systemsIn addition to this, our mobile plant fire suppression systems have been tested to Original Equipment Manufacturer and International Electrotechnical Commission (IEC) standards for bump, shock, vibration, and temperature performance by a UKAS accredited testing facility.
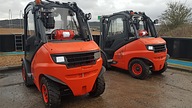
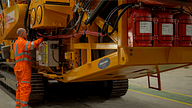
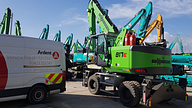