Focus On: Forklift Fire Suppression Systems
Forklift fire suppression system focus
Small plant machinery such as forklifts are critical equipment in many businesses. So when a forklift fire occurs, it can have serious consequences that go beyond machine repair or replacement costs.
Since forklifts often operate inside buildings like warehouses, a forklift fire can cause serious disruption to operations, as well as damage or loss of materials and finished products which may be stored in the vicinity. More serious still is the risk of injury to operators and other staff working in the building.
Regular maintenance practices can help reduce the chances of a forklift fire breaking out, but accidents still happen, and the risk of fire cannot be eliminated. A forklift fire suppression system is designed to protect the equipment, facilities, and operator if a fire occurs. And they have high success rates, but they must be the right system for the specific machine and environment.
What are the main fire hazard areas in Forklifts?
A common cause of fires in forklifts are flammable materials (such as dust, debris, oil, and grease) getting in contact with very high temperature components in the engine compartment (such as engine blocks and manifolds), then igniting. Electrical short-circuits can also be a cause of fire ignition.
Accumulating in the engine compartment, the build-up of flammable materials in forklift trucks poses a significant fire risk - particularly in industries such as waste and recycling, in paper and timber yards where large amounts of combustible materials are handled daily. If a broken fuel or hydraulic line sprays diesel or oil onto a superheated engine component, this can also start a fire.
What are the requirements for an effective forklift fire suppression system?
The size of forklift trucks means they need a compact but efficient forklift fire suppression system, without compromising on system quality or reliability.
There are plenty of forklift fire suppression system manufacturers offering fire protection, but not all these systems are reliable and fit for purpose - often struggling with issues arising from high rates of false discharges, which put machines out of action and cost organisations money.
In addition to linear heat detection cable, an effective forklift fire suppression system needs distribution nozzles to discharge the extinguishing agent, directly targeting all the main hazard areas in the engine compartment. These systems will protect all high-risk areas in the case of a fire rapidly expanding from its initial ignition point.
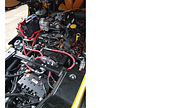
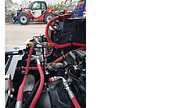
Agent distribution network and nozzles covering all main fire hazards in an effective forklift engine compartment.
ABC dry chemical, also known as dry powder, is the recommended extinguishing agent for a forklift fire suppression system, as it offers excellent fire knock-down capabilities. Dry powder is also able to disperse widely and cover even the hardest-to-reach areas of the engine compartment.
Dry chemical agents can be used independently or in combination with wet chemical agents. Wet chemical is recommended where the forklift operates in environments with abundant combustible materials, since it helps prevent fire re-ignition. The wet chemical cools superheated components, stopping combustible materials from re-igniting after the system has put out the fire.
Why our forklift fire suppression systems are superior
As previously mentioned, there are plenty of forklift fire suppression systems in the market offering forklift protection. However, a significant number of them use pneumatic tubing systems. Trapped, kinked, or otherwise damaged tubing will release the pressure in the tube, discharging the system. High instances of false discharges in these systems mean increased vehicle downtime and operational disruption.
Our forklift fire suppression systems use a linear heat detection cable that eliminates the risk of false discharges due to loss of pressure, ensuring 24/7 reliable protection for the forklift, facilities, and operators. These systems can differentiate between a fire and a cut or damaged detection cable, and will only activate the system in case of a fire. If damage to the detection cable is identified, the control module will report a fault in the system.
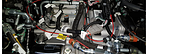
Linear heat detection cable (red) routed around fire hazards in forklift engine compartment.
What other system features are recommended for forklift fire suppression systems?
- An engine shutdown function is always recommended. When a fuel or hydraulic line fails, it can spray flammable liquid onto superheated components and cause a fire. Shutting down the engine stops fuel intake and the continual fuelling of the fire. This significantly reduces the chances of fire re-ignition. Remember - a forklift fire suppression system only gets one chance to put out a fire.
- An effective forklift fire suppression system can also include a battery isolator, which can also help avoid fire re-ignition when the source of the fire is an electrical short-circuit.
Finding the perfect forklift fire suppression system
Forklift trucks aren’t the only asset at risk if a fire breaks out. If a fire isn’t contained, it can spread to the area surrounding the forklift, including the facility and stock, put operators in danger, and result in costly downtime.
A forklift fire suppression system fitted to the plant is the best protection against the potential effects of a fire. The effectiveness and reliability of the system will vary significantly depending on the fire detection and agent distribution methods that the system employs, among other parameters.
For more information on how to protect your forklifts and other equipment against the risk of fire, contact one of our experts on 01423 326740 or send us a message to request a call back.