BS 6164:2019 – Fire Suppression for Tunnelling
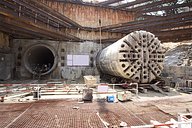
The British Standard (BS) 6164:2019 came into effect on 31 October 2019. This British Standard is a full revision of the now-superseded BS 6164:2011 with regards to health and safety in tunnelling in the construction industry.
Clause 13 of BS 6164:2019 contains guidance and recommendations regarding fire protection of plant and equipment used in tunnelling. It refers to the protection of both mobile and static equipment, including specialised tunnel plant intended for underground use and surface equipment that can be taken underground.
Specialized tunnelling plant requiring fire protection includes tunnel boring machines (TBMs), roadheaders, tunnel excavators and dump trucks, locomotives and access platforms amongst other. Surface plant that can be taken underground comprises earthmoving machinery such as surface excavators and dump trucks, mobile elevating work platforms (MEWPs) and static equipment like concrete/group pumps, transformers, generators and compressors.
All these pieces of equipment include fire hazards that can pose a risk of fire. Heat, fuel and oxygen are the three elements a fire needs to ignite. Mobile equipment usually contains large amounts of fuel and is also a source of heat (see Table 1). A leak in a diesel or hydraulic line can spray flammable fluid onto hot components, starting a fire. Debris that accumulates around the engine compartment and the belly pan can also ignite when in contact with a heat source. Electrical fires can also occur when heat generated by an electrical source encounters a source of fuel.
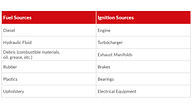
TABLE 1 – FUEL AND IGNITION SOURCES IN TUNNELLING EQUIPMENT
Fire suppression systems are installed in plant and equipment to protect the operator, equipment and facilities against the risk fire. However, not all systems in the market offer the same level of protection as the design parameters and capabilities vary significantly from system to system.
This blog post aims to help anyone with an interest or responsibility for the protection of plant and equipment used in tunnelling to understand the key principles behind the current generation of fire suppression systems. In addition, it examines the main aspects to be considered when choosing a fire suppression system in line with BS 6164:2019.
Fire Suppression System Design
On-board fire suppression systems consists of four major components:
- A detection system to provide automatic fire detection, usually linear heat detection, spot detectors, infra-red flame detectors, or a combination of the same.
- An actuation system operated manually and/or automatically.
- A tank or several tanks to store the suppression agent.
- An agent distribution network which delivers the agent from the tank through hydraulic hose and fixed nozzles to the fire hazard areas.
If an automatic actuation system is not installed, the system can only be activated manually. Relying purely on a manual system usually leads to a slower reaction to fire. A combination of automatic and manual actuation is recommended to achieve higher levels of reliability.
Fire suppression systems are not designed to extinguish all fires, especially when unusual amounts of combustible material are present or in areas that cannot be covered by the system, such as pneumatic types. It is therefore highly recommended to supplement the fire suppression system with portable hand-held fire extinguishers located on-board the vehicle.
Fixed fire suppression systems are designed following a local application or total flooding method. Local application systems are recommended for mobile plant such as excavators and dump trucks. When designing a local application system, each individual hazard area is identified through a fire hazard analysis and the quantity of extinguishing agent, number of discharge nozzles and nozzle location is chosen to give proper coverage. Individual hazard protection is key for system efficiency in heavy mobile equipment, where the hazards are not located in an enclosure and air flow can affect the effectiveness of the system.
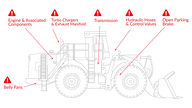
IMAGE 2 – FIRE HAZARD AREAS IN WHEEL LOADER
Total flooding, also referred to as volume protection, is only applied when the fire hazards are located in an enclosed space, such as a generator or an electrical cabinet. This method of fire protection works by introducing a sufficient quantity of suppression agent throughout the volume of the enclosure to suffocate the fire.
Extinguishing Medium
BS 6164:2019 recommends a variety of suppression agents for fixed fire suppression systems, depending on the nature of the plant or equipment to be protected.
Heavy mobile plant
ABC dry chemical, also know as dry powder, is currently the most widely used agent in the vehicle fire suppression market to protect heavy mobile plant. On a weight basis, it is the most effective agent in suppressing fires and provides rapid fire knockdown. It is effective against Class A, B and C, as well as electrical fires, covering all the fuel sources present in mobile plant.
Dry chemical works by coating the fuel source with a thin layer of powder, separating the fuel from the oxygen in the air. The powder also works to interrupt the chemical reaction of fire. Due to its fine powder form, it also disperses easily to cover even hard to reach areas, aiding coverage of the fire hazard areas.
BS 6164:2019 also refers to the need for cooling to prevent fire reignition. Reignition can occur after fire suppression system discharge due to the extremely high temperature of vehicle components such as turbochargers and exhaust manifolds. Diesel has an auto-ignition temperature of 220 °C; in order to prevent fire reignition it is necessary to reduce the surface temperature of components below this critical temperature. This can be achieved by using wet chemical suppression agent, which provides cooling of superheated components to below 220 °C, significantly reducing the risk of fire reignition.
A twin agent fire suppression system combining dry and wet chemical suppression agents is therefore the optimal solution for mobile plant fire protection. The dry chemical offers rapid fire suppression and excellent coverage, while the wet chemical provides cooling to prevent fire reignition after system deployment.
Static equipment and enclosures
Enclosures such as electrical cabinets, generators and transformers can be protected with a clean agent fire suppression system. These systems disperse an inert gas to suppress the fire, using a total flooding application method. They work by reducing the oxygen in the enclosure below the level required for combustion. Clean agent is electrically non-conducting and leaves no residue upon evaporation.
Fire Detection and System Activation
Even the most effective suppression agents depend upon a rapid and reliable fire detection and activation method to trigger the fire suppression system. The most common form of fire detection used in fire suppression is heat detection, including spot heat detectors, electronic linear heat detection cable and pneumatic linear heat detection tubing.
Heavy mobile plant
Mobile plant such as excavators and dump trucks are subject to significant shock and vibration during operation. This is major concern to anything that is installed in the vehicle, including fire suppression systems, as it can lead to system failure.
Pneumatic linear heat detection tubing uses a tube pressurised with nitrogen, which bursts when exposed to fire temperatures, activating the system. Tube pressure leakage is common in these systems, and damage to the tube (trapped, kinked or cut tube) can cause false system discharges. These false discharges are common in pneumatic fire suppression systems installed in heavy mobile plant as the shock and vibration exposes the tube to harsh operating environments.
Electronic fire suppression systems using linear heat detection cable provide the most reliable protection for off-road vehicles, as they are designed to withstand the level of shock and vibration common in these environments. These systems significantly reduce the chance of false discharges in comparison to pneumatic systems, as they are able to differentiate the electrical signal resulting from a fire from the signal from damage to the detection cable. Only a fire will melt the heat sensitive polymer that separates the conductors. Once the polymer melts, the conductors initiate contact with one another and communicate with the control module to discharge the system.
Static equipment and enclosures
As static equipment is not exposed to the levels of shock and vibration common in mobile plant, a pneumatic fire suppression system using linear heat detection tubing can be used, providing a more cost-effecting solution for enclosure fire protection.
A Note: Fire Prevention
A fire suppression system is the best way to protect equipment against a fire. However, good equipment maintenance practices can help reduce the chances of a fire in the first place. Regular maintenance checks and procedures are strongly recommended to help reduce the risk of equipment fire. These include keeping equipment clean both internally and externally, regularly inspecting the primary ignition points, checking for wear and tear of diesel, hydraulic fluid and electrical lines, tightening loose connections, and inspecting the braking system for proper adjustment, especially if the brakes overheat when not engaged.
For more information on fire protection for tunnelling plant and equipment, contact our experts today at [email protected], or call us on +44(0)1423 326740
Related News
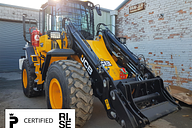
Ardent Receives P-Mark SPCR 199 Certification
We’re proud to announce that we have obtained the latest version of P-Mark SPCR 199 certification for the Ardent Dual Agent Systems.
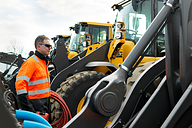
What Makes For a Trouble-Free Fire Suppression System?
How can installation standards save money in the long term?
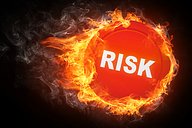
Hazard Analysis - Why Do One?
You're only as strong as your most serious hazard.